카파(CAPA) 파트너로 활동하는 각 분야 최고 제조 전문가를 소개하는 <카파 파트너스> 인터뷰 시리즈. 이번에 소개해드릴 ㈜조이는 디자인을 공부한 아들과 PCB 설계 경력 47년의 아버지가 의기투합해 설립한 PCB 설계 전문업체입니다.
지난 19일 방문한 경기도 부천 소재 PCB 설계 전문업체 ㈜조이의 사무실. 한쪽 벽에 붙어있는 낡은 모터가 눈에 띄었다. 모터가 담겨있는 봉지 겉면엔 '112,000'이라는 숫자가 적혀 있었다. 숫자는 이 모터에 전원이 잘 공급되는지 확인하기 위해 테스트를 실시한 횟수를 의미한다. “우리는 미스(miss)가 거의 없다”는 회사 관계자의 말을 실증적으로 뒷받침해주는 숫자다.
㈜조이 사무실에는 PCB 설계 경력이 50년 가까이 된 아버지와 3D 프린팅에 매료된 MZ세대 아들이 함께 출근한다. 아들이 사장을 맡아 회사를 운영한 지 5년째. 아들이 아이디어를 내면, 아버지가 설계를 한다. 아버지가 설계한 PCB 기판을, 아들이 출력한 3D 프린팅 시제품에 조립해 문제가 없는지 확인한다.
PCB 설계와 3D 프린팅, 오랜 경험에서 나오는 베테랑의 경험과 젊은 사장의 패기가 환상의 호흡으로 빛을 발하는 회사, (주)조이가 이번 카파 파트너 인터뷰의 주인공이다.
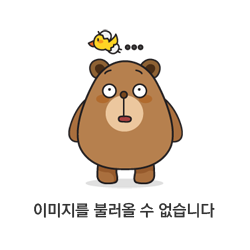
대표를 맡고 있는 1991년생 조영재 대표는 대학에서 인테리어 디자인을 전공했다. 대학교 때 건축 구조물을 만들던 도중, 우연히 3D 프린팅에 관심을 갖게 됐다고 했다. 건축 구조물은 벽을 하나하나 만들어서 세워야하는 데 반해, 3D 프린팅은 전체 건축물을 한 번에 출력해냈다. 이 점이 조 대표의 흥미를 끌었다. 이후 인테리어 회사에 취직해 일을 하던 중에도 틈틈이 3D 프린팅을 공부하며 사업 계획에 몰두했다. 결국 지난 2015년 아버지와 함께 사업을 시작했다. 본인이 직접 설계까지 배워 어엿한 PCB업체 대표가 됐다.
조영재 대표의 부친 조창현씨는 50년 가까이 한 세월을 PCB 설계 일을 해온 베테랑이다. 17살 때부터 PCB 설계 일을 시작해 PCB 경력이 올해로 47년에 달한다. 삼성전자가 막 반도체 시장에 뛰어들던 시기에 PCB업계에 입문한 조씨는 1983년엔 일본의 산요(SANYO) 전기에 입사해 본격적으로 PCB 설계 업무를 맡아 한 분야에서 진득하게 경험을 쌓았다. 이제는 사업하는 아들이 맘 편히 의지하는 든든한 버팀목이자 (주)조이의 가장 큰 자산이다. 조영재 대표는 “아버지와 함께 사업을 시작한 이후로, 설계를 못해서 거절한 거래는 단 한 건도 없다”고 말했다.
다음은 이들 부자와의 일문일답.
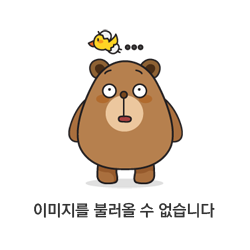
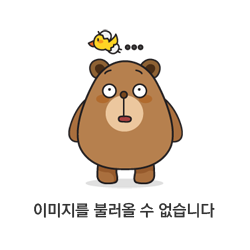
Q) PCB 설계와 3D 프린팅을 접목한 게 인상적이다
“PCB 설계와 3D 프린팅이 접목되는 것이 낯설게 느껴지실지 모르겠다. 하지만 PCB 보드는 결국 제품 케이스와 함께 조립되어 양산할 수 있어야 완제품으로서 의미가 있다. PCB 보드만 만든다고 끝이 아니다.
PCB 보드는 납작하지만 부품 자체가 갖고 있는 높이나 크기가 있다. PCB 보드를 제품 케이스 안에 넣었을 때 부품의 높이 때문에 조립이 안 되는 경우도 종종 있다. 제품의 완성된 형태까지 고려하지 않아 발생하는 문제다. 이런 경우를 방지하기 위해 3D 프린팅으로 시제품 케이스를 출력한 뒤 그 안에 PCB를 넣어 조립까지 마무리해본다. 제품을 만드는 공정을 보면 설계, 개발비가 (중요한) 비용이지만 목업을 만드는 비용 또한 상당하다. (케이스 제작을 위해) 금형을 만들어야하는 경우에는 비용이 수 백만, 수 천만 단위 아니냐. (주)조이에서는 3D 프린팅으로 사전에 문제를 점검하고 수정해서 비용을 절감할 수 있다."
조 대표의 말처럼 PCB는 사전에 오작동을 걸러내지 못하면 양산 단계에서 엄청난 비용 손실로 이어질 수 있다. 그만큼 사전에 오작동 여부를 잡아내는 것이 중요한 경쟁력이다.
Q) PCB 설계 단계에서 오작동을 검수하는 남다른 노하우가 있나
“직접 지그(JIG)를 만들어서 테스트해보는 것이다. (주)조이에서는 지그를 직접 만들기 때문에 비용도 상대적으로 저렴한 편이다. 지그를 (외부업체를 통해) 따로 제작하면 비용이 최소 몇 십만원에서 몇 백만원까지 든다.
PCB를 지그에 놓고 전원을 공급해서 잘 작동하는지 반복적으로 테스트한다. 많게는 11만 2000번까지 테스트해봤다. 기능적으로 A동작으로 설계한 결과가 A동작으로 나타나는지를 확인한다. 가끔 A동작으로 설계했는데 B동작의 결과가 나오는 경우가 있다. 작동의 정도가 1이 작동해야하는데 3만큼 작동하는 오작동 케이스도 있다.
육안으로도 검사를 한다. PCB 쇼트가 불량인 경우 분리돼 있어야 할 납땜 부위가 서로 붙어있다. 니퍼로 따로 떼어내는 수작업을 해서 보완한다.
(그래도 불량이 생기면?) 불량 사항이 없을 때까지 반복해서 테스트하고 100% 완벽한 제품이 나왔을 때 고객 분들께 말씀드리는 것이 저희 일이라고 생각한다.”
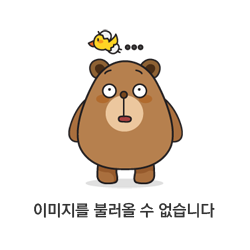
Q) PCB 설계상에 문제가 있는 제품들도 적지 않을 것 같다
"㈜조이에서 자체적으로 개발한 제품 중에 새니타이저를 자동으로 공급해주는 ‘꾹이’라는 제품이 있다. 센서로 손을 감지해서 새니타이저를 자동으로 짜주는 제품이다. 처음 설계했을 때는 새니타이저 분출구 쪽에 IR 센서가 1개만 있었다. 사용 테스트를 하다 보니 오작동의 소지가 있었다.
IR 센서는 빛을 감지해서 작동한다. 새니타이저가 나오는 주입구가 돌아가서 센서를 가리면 손을 전혀 인식하지 못하는 문제가 생기더라. 센서를 주입구 양쪽에 총 2개를 달아서 센서가 가려지지 않도록 하고 동시에 손을 더 잘 인식할 수 있도록 설계를 수정했다. 센서가 1개만 있었다면 금형까지 제작을 완료했을 때 금형 비용을 버리는 셈인데 이를 예방한 것이다.
(센서의 오작동을 일으키는 또다른 사례가 있나) 현관문에 센서 조명이 있지 않나. 사람이 지나갈 때만 센서 조명이 켜져야하는데, 가끔 사람이 없어도 조명이 켜지지 않나. 센서가 감지할 동작이 없는데도 작동하는 거다. 그런 문제들은 센서등 제품을 양산하기 전에 발견해서 설계를 수정해서 판매해야 한다.”
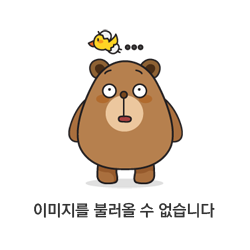
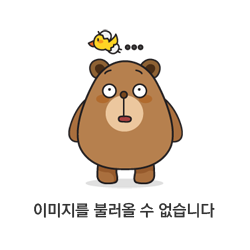
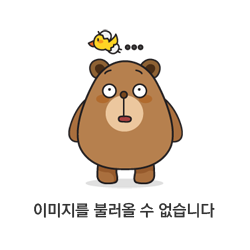
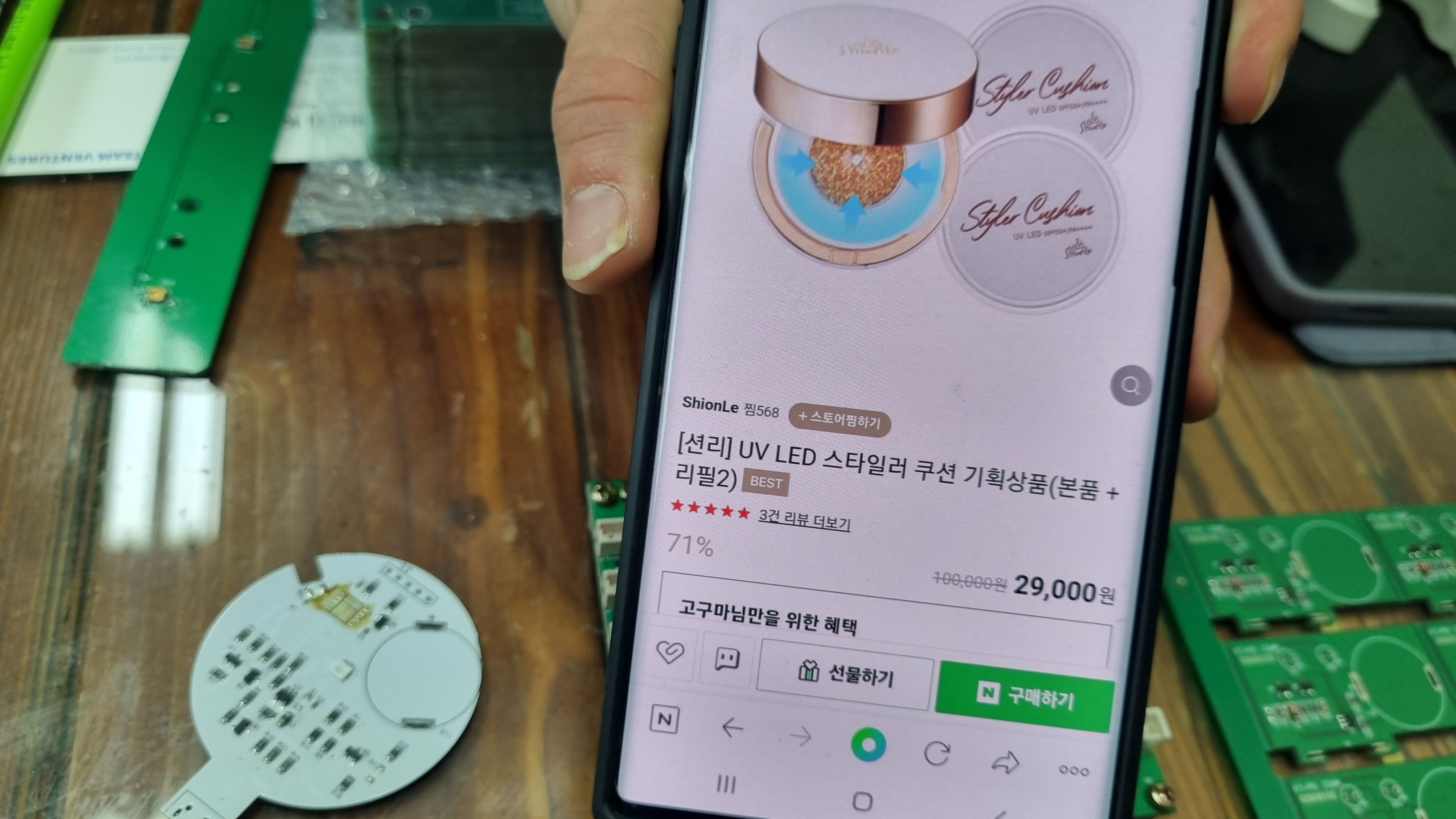
Q) 특히 어려웠던 제품이 있다면
“다른 업체에서 생산을 하다가 오작동이 생긴 제품이었는데 개선 요청이 들어왔다. (확인해 보니) 발열의 문제가 있었다. 불이 날 뻔하기도 하고 PCB 주변의 사출물이 녹아버리는 문제가 있었다.
회로도도 없고, 데이터도 없었다. 그저 완제품 PCB만 가지고 오셔서 해결해달라고 하시니 난감했다. PCB를 뜯어볼 수도 없는 노릇 아닌가. 그래도 사용하는 부품의 전원부터 한 단계씩 문제를 찾아 들어갔다. 패턴을 짚어가면서 문제를 확인했다. 과전류를 먹는 부분, 전압이 불안정한 부분들을 하나하나 찾아냈다. 과전류가 발생하면 열이 난다. 계측기로 짚어 보고 열화상 카메라로 촬영도 한 끝에 문제의 원인이 된 부품을 찾아냈다. 결국 부품을 작은 PCB판으로 교체했다.”
Q) 초보 운전자들에게 유명한 유튜버와도 협업했던데
“차폭을 체감하지 못하는 초보 운전자들에게 도로 차선을 안내해주는 제품을 만들었다. 자동차 대시보드 위에 올려놓으면 운전자의 시야에서 볼 때, 차선 도로가 LED 빔으로 앞 유리에 쏘아진다. 이 제품은 조도 센서로 작동하는데 눈부심 방지를 위해 외부 환경의 밝기에 따라 LED 밝기를 스무스하게 조절해준다. 밝기가 급격하게 낮아지거나 높아지면 운전에 방해가 될 수 있어서 ‘언덕길에서 구슬 굴러가듯’, 밝기 정도가 스무스하게 조절되는 것이 특징이다.”
㈜조이의 고객군은 몹시 다양하다. 주문 요청도 특별히 가리지 않는다고 했다. 조 대표는 "(주문을 받는 제품군이) 화장품 진동 쿠션 퍼프, 해빙기, 호텔 카드키 및 초인종 등 마스터 제어 시스템, 자동 손소독기 디스펜서 등 다양하다"고 말했다. 특히 최근엔 젊은 창업자들로부터 주문을 받는 사례도 많다고 했다.
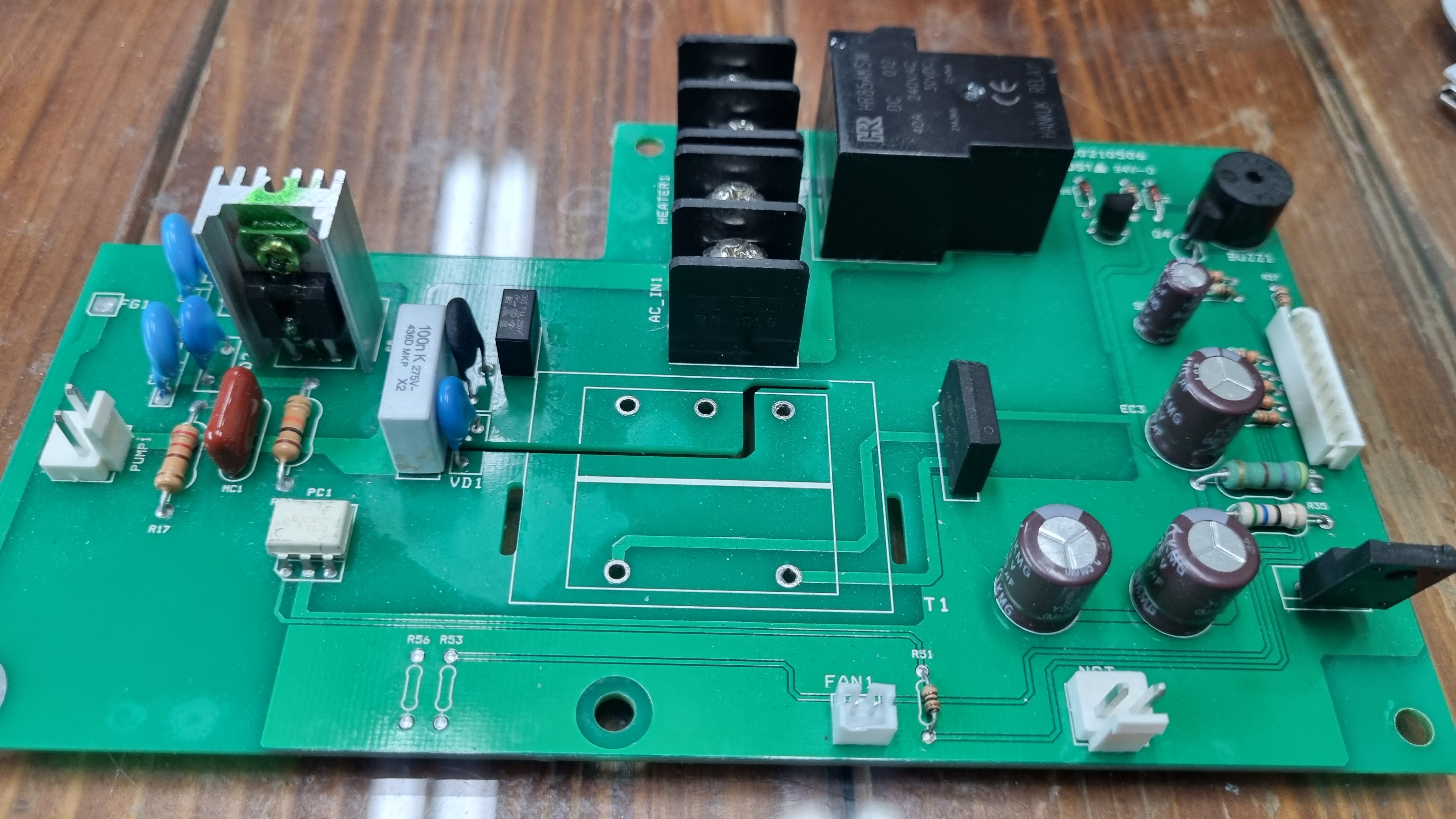
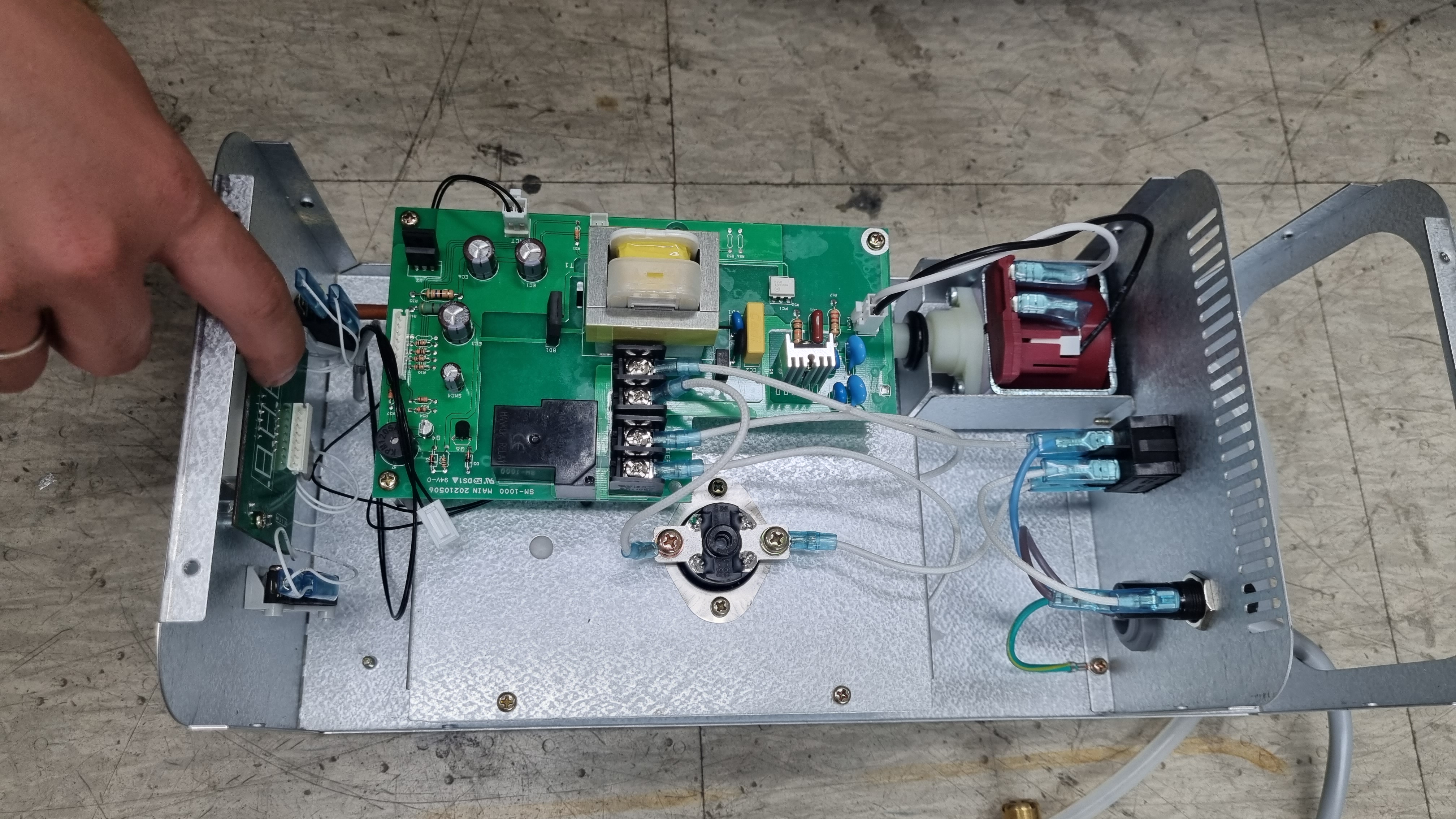
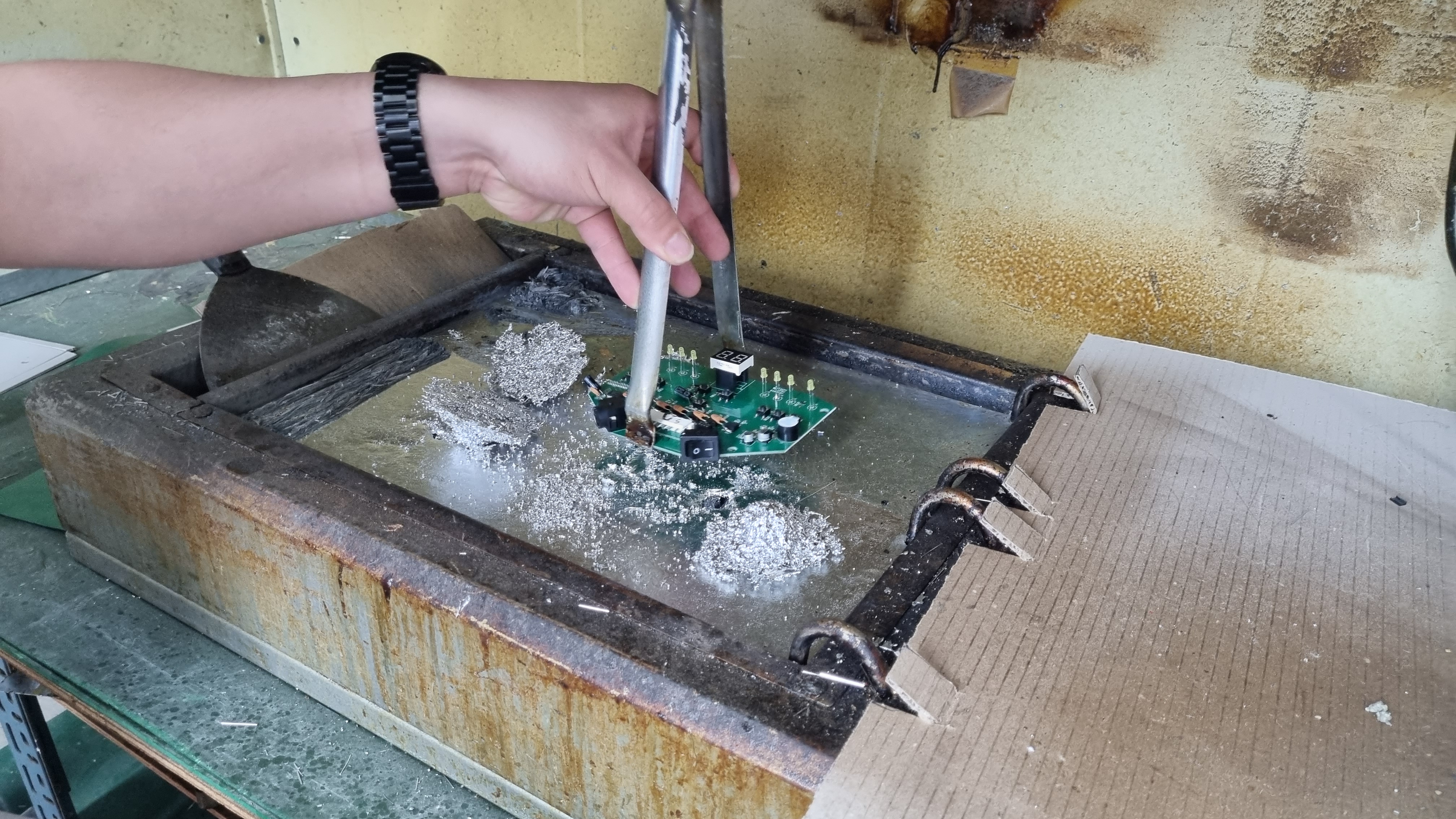
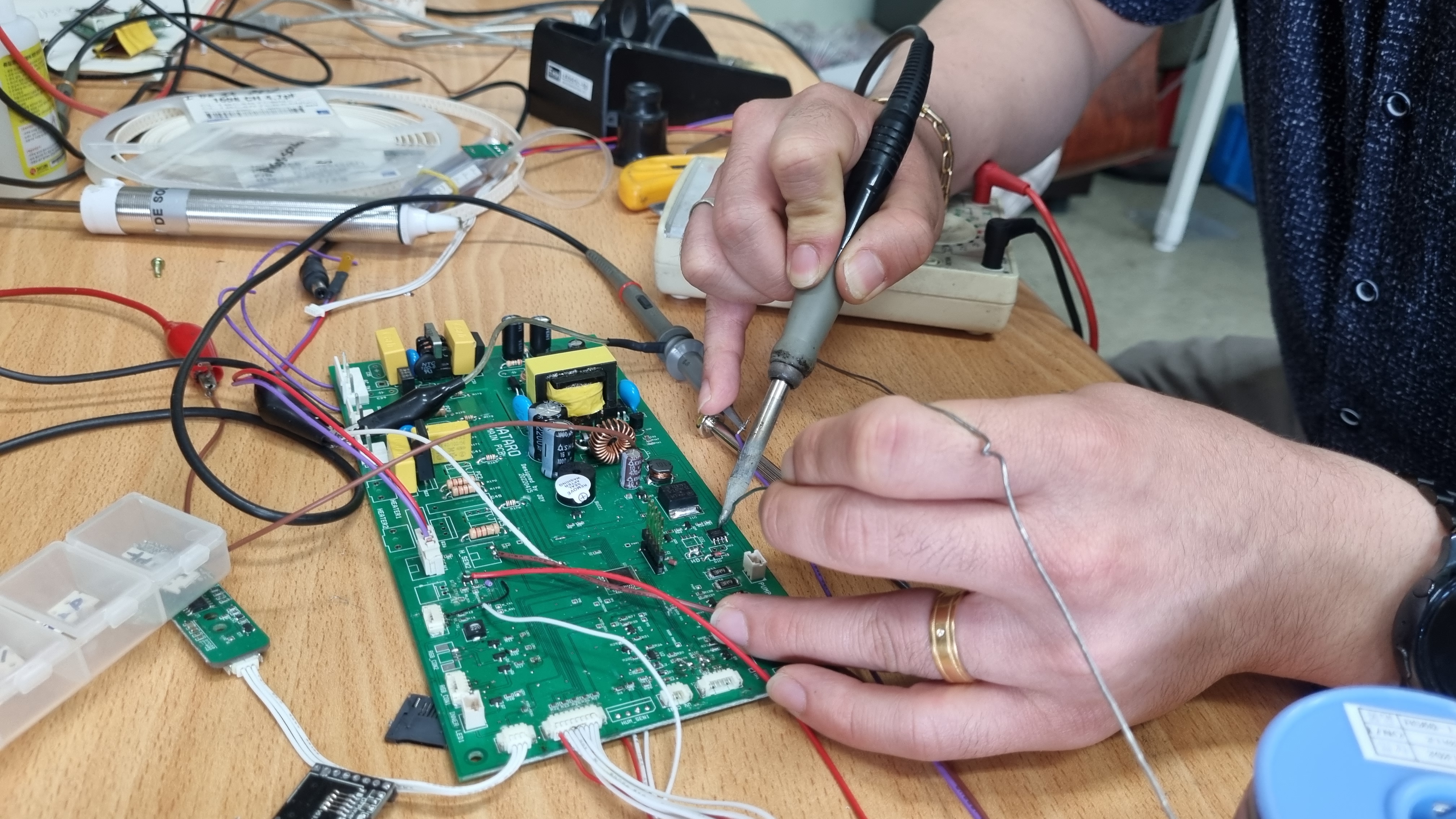
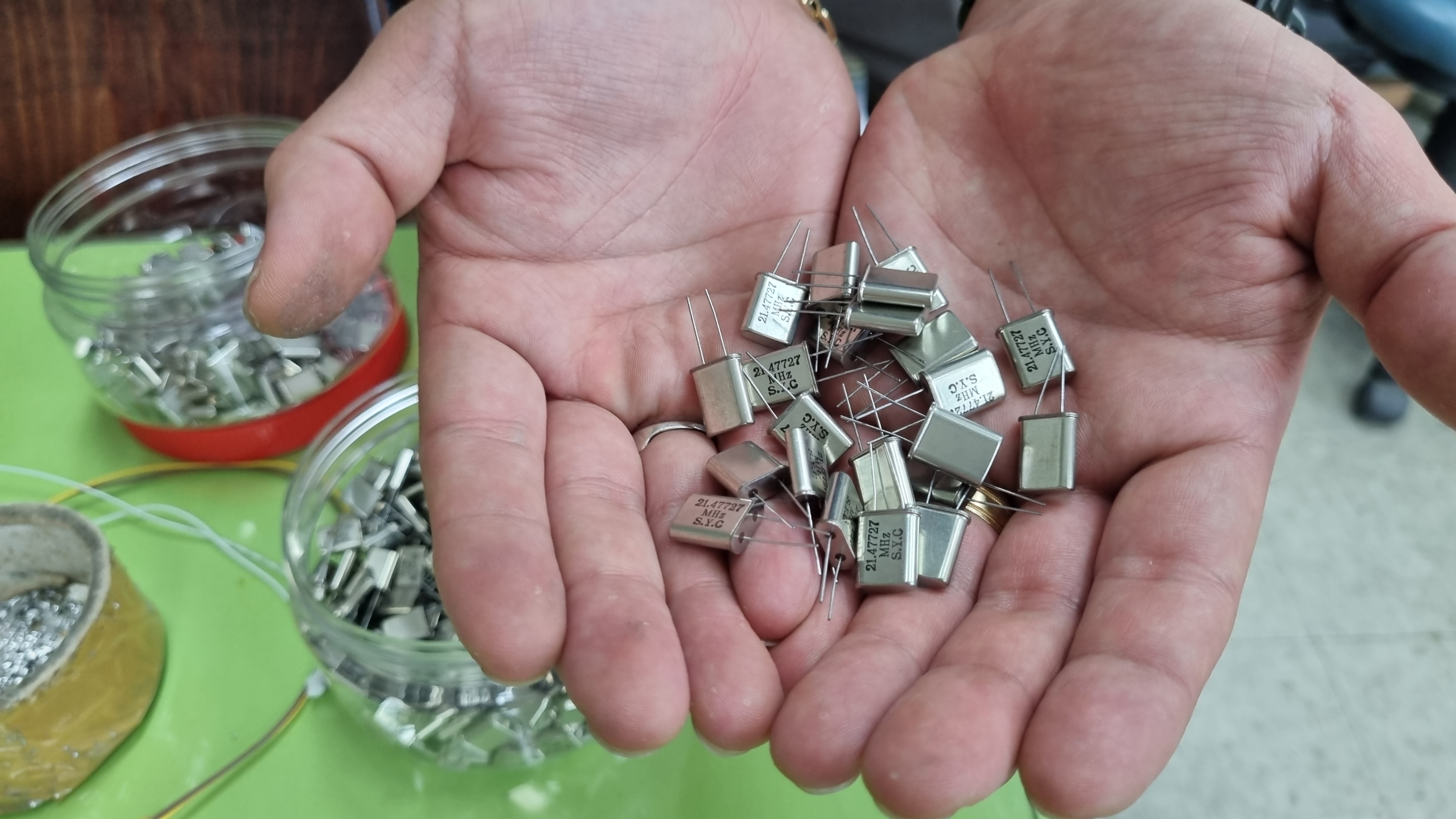
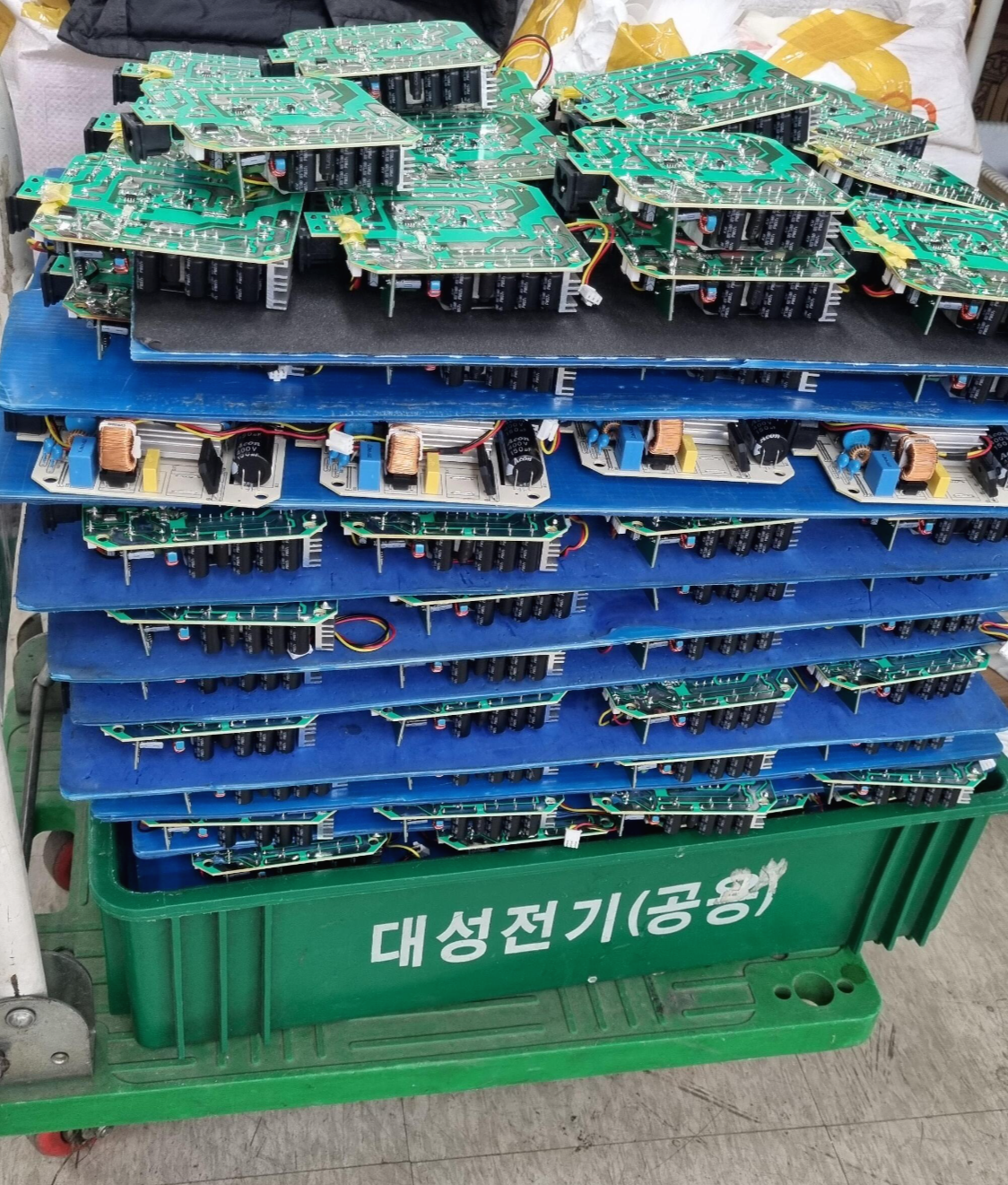
Q) 함께 작업한 창업자 가운데 기억에 남는 사례가 있다면
“최근에 저희 업체를 통해 제작한 제품을 와디즈에서 펀딩을 받아 양산에 성공하신 고객 분이 있다. ‘피오유엘’이란 회사에서 만든 ‘바이플라’라는 무필터 공기청정기다. 설계부터 완제품 생산까지 6개월 정도 함께 고민을 나눴던 제품이다. 세상에 없던 제품이 태어나기까지는 최소 수 개월에서 수 년까지, 많은 사람들이 한 제품에 대해 고민을 나눠야하고, 제작을 위해서는 협업을 해야 한다. 그렇기에 제품 하나가 만들어지면 뿌듯한 건 당연하다. 젊은 창업자 분들이 저희와 함께 수 개월 머리 싸매고 고민하던 제품이 세상의 빛을 보는 일은 매번 벅차다.”
Q) 제조 전문가로서 이루고자 하는 꿈이 있나
“거창한 꿈이긴한데.. 말해도 되려나(웃음). 제조 산업을 전체적으로 봤을 때, 고객 분들이 '더 이상 양산 제품도 중국에 가서 만들 필요가 없구나' 하고 깨닫게 해드리고 싶다. 국내 제조업체 분들은 해외업체와 비교했을 때 훨씬 높은 수준의 전문성과 기술력을 갖고 계신다. 제품 설계부터 제작 초기에는 국내에서 제품을 만드시다가, 결국 값싼 비용 때문에 중국에서 양산하는 경우가 다반사다. 과거에 삼성전자의 협력업체로부터 수주 받아 만들었던 갤럭시 S10 광고판도 처음엔 저희가 만들었다. 그런데 결국 베트남 가서 만들더라. 저희가 더 좋은 제품을, 더 적절한 가격에 만들어드릴 수 있으면 언젠가 그런 날이 오지 않겠나. 저희 자리에서 최선을 다하겠다.”
5년 차 CEO 조영재 대표에게 앞으로 회사를 어떻게 운영할 생각인지 묻자, 조 대표는 검지 손가락을 관자놀이에 짚고 신중하게 고민하다가 아래처럼 답변을 내놨다.
양심적으로 일하고 싶다.
고객 분들이 여러 업체 전전하면서 고생하시지 않도록 해드리고 싶다.
믿고 맡기실 수 있게, 먼저 믿음을 드리는 업체가 되도록 노력하겠다.
정직하게 일하겠다는 조영재 대표의 말에서 어쩐지 묵묵히 옆에 앉아있던 부친 조창현씨의 삶의 흔적이 엿보이는 듯했다. 50년 가까이 한 세월을 PCB 설계 전문가로 살아온 조창현씨는 인터뷰 자리에 함께했지만, 아들이 뭔가를 묻기 전까지는 단 한 번도 먼저 입을 열지 않았다. 그저 자리에서 묵묵하고 성실하게 살아온 아버지의 세월을 물려받아 아들은 자신의 경영 철학으로 삼은 듯했다. 웃는 모습이 특히나 닮은 부자, 아들이 주인공이 될 수 있도록 자리를 비켜주는 아버지의 모습을 보며 아들 또한 말보다 실력으로 승부하는 전문가로서의 삶의 궤적을 밟아가지 않을까 생각했다.
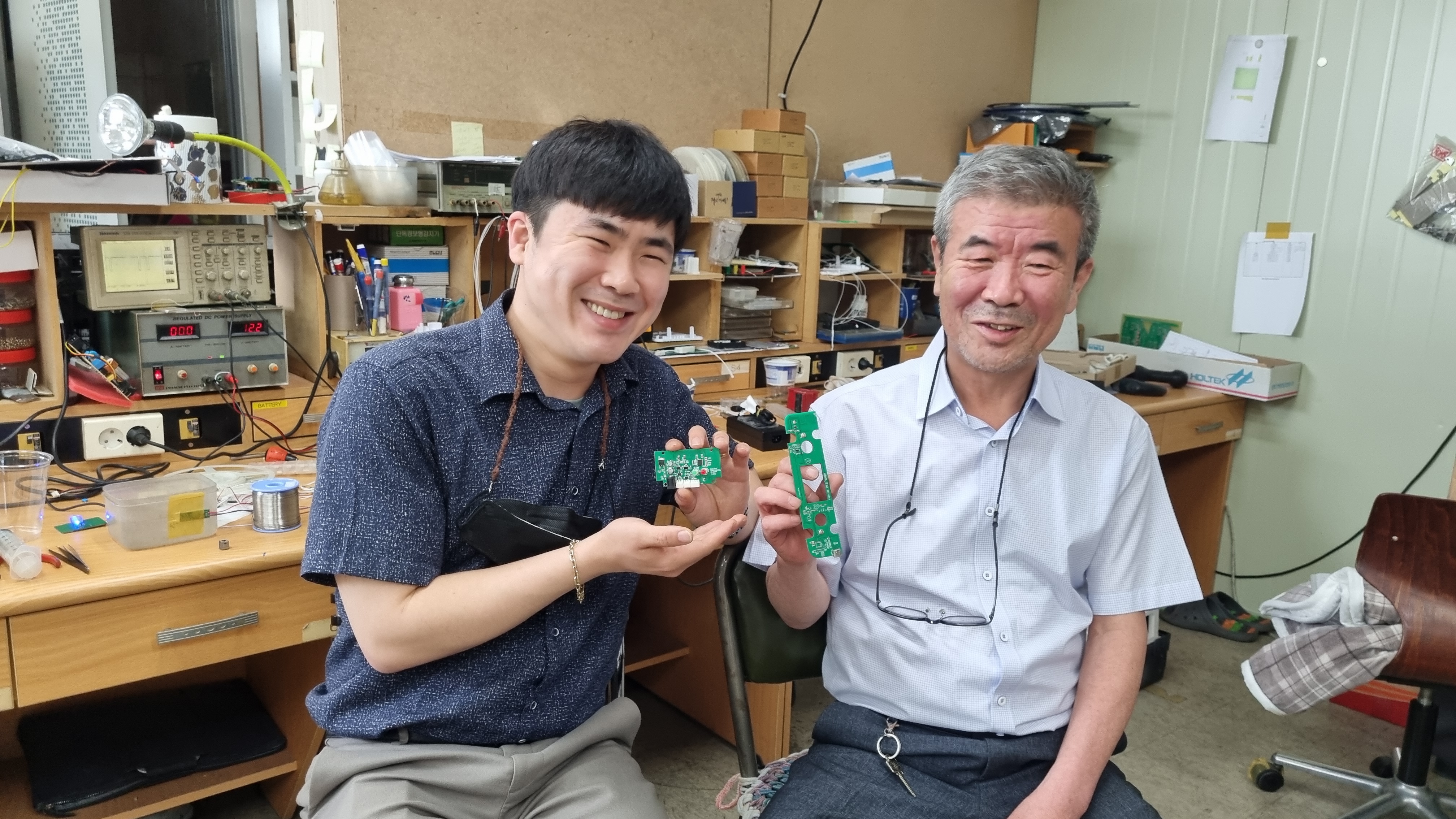
제조업체 매칭플랫폼 카파(CAPA)에서는 ㈜조이를 비롯해 PCB 분야에서 최고의 경쟁력을 보유한 전문 파트너(제조업체)를 만날 수 있습니다. 아래 링크를 통해 지금 카파를 방문해 보세요!

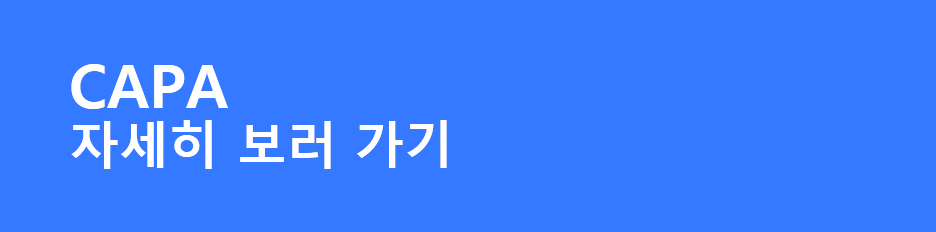
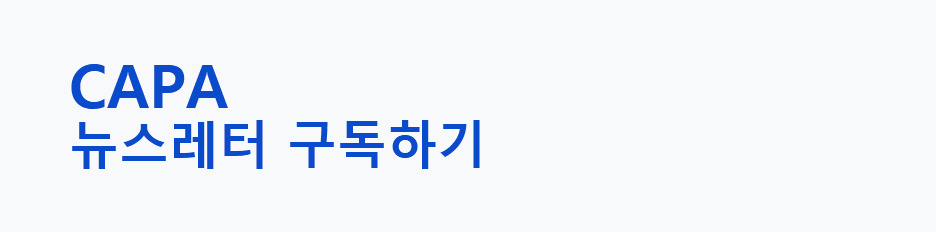
'캐파 (CAPA) > 캐파 파트너스' 카테고리의 다른 글
[카파 파트너스] (주)썸잇(기구설계) (0) | 2022.07.04 |
---|---|
[카파 파트너스] 미르 (플라스틱 CNC 목업) (0) | 2022.06.03 |
[카파 파트너스] (주)리텍(양산 금형) (0) | 2022.05.06 |
[카파 파트너스] 소프트몰드(QDM금형사출) (0) | 2022.04.12 |
[카파 파트너스] 에이스캠엔지니어링(시제품 제작) (0) | 2022.04.04 |